Behind the scenes at Gretsch's awe-inspiring Custom Shop
Master Builder Stephen Stern gives us the lowdown on what it takes to build the legendary company's high-end guitars
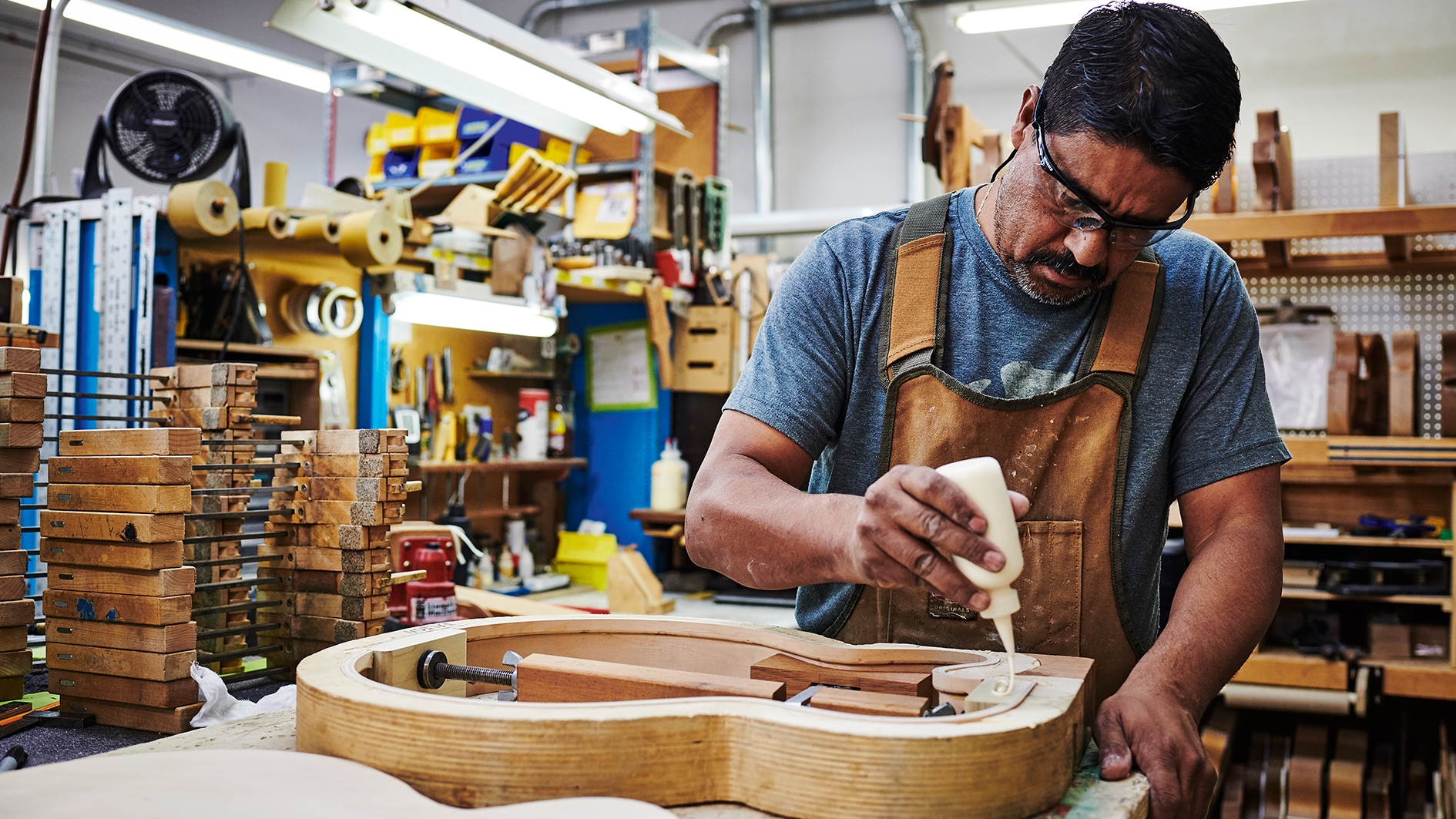
Stephen Stern learned from the best. In 1994, during his tenure with the Fender Custom Shop, he earned the title of Master Builder before going on to develop his skills as an archtop luthier.
This led Stephen to the Gretsch Custom Shop where he and his team continue to practice the fine art of building these legendary guitars. We delve deeper into the story...
How did the Custom Shop start out?
“Back in 2001 or so Yuriy Shishkov and I started doing the [archtop] Benedettos, and we had a couple of guys helping us. And then the Gretsch Custom Shop started in 2004 with two models: the White Falcon and the 6120, the ’55 model. So they were doing those downstairs, and then we moved upstairs to this workshop.
"I don’t know who made the decision or how it happened, but they said, ‘Well, let Stephen incorporate that with the Benedettos.’ Which made a lot of sense to me. So that’s what happened. And then Yuriy eventually moved back downstairs, so it was down to me [laughs] and I had a crew of about nine guys.
"We were doing about eight Benedettos a month and about eight Gretsches - so it was a lot.
“Eventually, Bob [Benedetto] moved on around 2006 or 2007 and opened his own place out in Savannah, Georgia, with a partner - so then I just had Gretsch. It was just the two models, and in time those kind of ran their course, you might say.
All the latest guitar news, interviews, lessons, reviews, deals and more, direct to your inbox!
"So then we started doing the Tribute guitars: the Brian Setzer and Billy Zoom. And we were just starting to get into the Eddie Cochrane Tribute when I got a couple of orders for some Duo Jets and Penguins and I told the guy that was doing the marketing, ‘I wish we could deal in Jets and Penguins.’
What’s really great about doing those guitars is you get to examine a piece of Gretsch history
"At the time, we were doing the Billy Zoom, and he didn’t want that to conflict with the Billy Zoom because that was a Sparkle Jet. But I didn’t think it would conflict - but anyway, what do I know? [laughs]
"Then, in 2008, we’d had a show here, a summer show. We set up the training room like a showroom. It had a bar, tables and chairs, you know? It was a little dark and it had nice lighting. So we had a display there and it was really put in place to launch the Gretsch Custom Shop as what it is today.”
We reviewed the Eddie Cochran Tribute guitars in Guitarist back then. The detail was impeccable...
“That was a fun project - I got to go to the Rock & Roll Hall Of Fame. However, you’re kind of limited in time and what you can really do. By contrast, we had the George Harrison [Jet] here at the workshop for three days, which was great.
"Actually, what’s really great about doing those guitars is that you get to see these historic guitars but also examine a piece of Gretsch history. For example, we were able to spec out replicas of original parts from these guitars that we can then incorporate on our other instruments, like the knobs, the strap knobs, little things like that.
“For example, we had Stephen Stills’ White Falcon in here. We were doing some repair on it and we saw that the knob was the ‘G Arrow’ type with the jewels. So, from that one knob, we were able to draw out three different historically accurate knobs: the arrow, the ‘G’ and then the arrow ‘G’ with the jeweling.
"These are subtle details, but for the people that are really into it, it’s important. We also got into things like the vintage-correct arm rest. When I first started doing the Penguin and I put an arm rest on it was, like, ‘Wow, this thing doesn’t fit; the arm rest’s not right.' So that was one of my first goals, to recreate that accurately.”
Many Custom Shops hunt around for original vintage guitars to examine to improve the accuracy of their vintage replicas. Was there a similar process here at the birth of the Gretsch Custom Shop?
“Yes, I was fortunate; I was able to go back to Savannah [Georgia, to Gretsch HQ] and I have the book, the Randy Bachman catalogue book [Gretsch Guitar Chronicle by Randy Bachman and Fred Gretsch], and I looked through that and I picked out, I don’t know how many guitars that I wanted to study.
"I know one was the Roundup, and two models of the Duo Jet and the Penguin. So I was able to go back to Savannah and take notes and take lots of specs and photos, and that really helped.
“Then also we did the George Harrison and then the Billy Zoom. I remember when we were doing the Billy Zoom, we were able to x-ray the interior to get that rout - he was adamant that it had to be the exact rout on the inside, because that’s part of the sound and everything. That kind of thing really helps a lot: it’s another detail that subtly differentiates us from the imports.”
Fender logos and hardware details changed a lot over the years. Is it even more complex with Gretsch?
When we started out, we had two headcaps that we offered - now we have a list like this long [laughs]
“Fender has a lot of different eras of logos - and, of course, Gretsch also has different eras regarding logos, too. For example, they had the script logo, which was on the first Duo Jets, which I think is everybody’s favorite. It’s so cool.
"Then they came out with a square ‘G’ logo, and then they changed to the round ‘G’ logo, and then the round G pretty much stayed around. With the Falcons, there wasn’t much change other than they changed from the vertical [logo] to the horizontal.
"But when we started out, we had two headcaps that we offered - now we have a list like this long [laughs] - different materials and that kind of thing, and that’s great.
“The same with the fingerboards. We originally had just two fingerboard [styles], and I remember when I took over, we used to put the fingerboards on the CNC and they would perimeter them and rout the fret slots - and then we sent them to the inlay guy.
"But you know, we’re kind of like the low man on the totem pole as far as numbers of guitars goes, so everything else [at Fender’s factory, which also incorporates Gretsch Custom Shop] came first in terms of priority for time on the CNC.
"So it was hard to get on and eventually I said, ‘Screw this, I’m just going to send the fingerboards to [inlay] guy, who was Ron Thorn,’ because he has the same CNC machine, so he can do the whole thing. So that was it: we sent him the fingerboards and he got it all ready to go.”
You can go any way: you can do traditional, vintage finishes or go crazy with the sparkles and the different colors
Fender necks were produced in various profiles over the years. How have you approached vintage neck profiles with the Custom Gretsches?
“I took some profiles of the necks of old Gretsches that I’ve had in here, but they’re kind of all over the place. So I picked a profile I liked and that felt comfortable. We offer it in a stock dimension and also a fatter version. But, ultimately, we’ve had orders for V-shape necks or U-shape profiles and that kind of thing, and we can do that.”
What are the standard design elements of a Gretsch neck?
“It’s a 12-inch radius. The necks are all made here from big chunks of mahogany.
"The old ones have the dovetail, and then they switched over to a tenon. But we mainly use the dovetail unless it’s on something like a ’62, that has the tenon.”
How about the construction of the arched tops of designs such as the 6120? What are the traditional Gretsch top-construction and bracing you’ll use?
“Depending on the year, they started with parallel bracing and then it went to the trestle bracing. The tops are typically three-ply laminate spruce, but we also get orders for solid, carved-spruce tops.
"We have some really high-quality European spruce left over from when we were making the Benedettos - for example, the Rich Robinson model that we’ve just completed had a solid-spruce top.”
What’s the most technically challenging Gretsch model to build?
“Well, those Country Gentlemans are pretty tricky with their mutes and everything.
"I don’t want to say they’re all pretty easy - they’re not easy. But anything’s easy if you do it a lot. That said, there’s always things that just come up: challenges that are like, ‘Man, how did that happen?’ Like that guitar hanging up over there - it just developed a little crack in the wood, and I was like, ‘How did that happen?’ So now we’ve got to strip it and see how we can fix it.”
Gretsch guitars are some of the most visually stunning instruments ever built. What are the main types of finish you work with?
“The Gretsch Orange on the 6120s is a stain, then with the paints we have the Cadillac Green and the Firebird Red - but we actually probably make more guitars in Fender colors at the moment.
"And I say this to everybody, what’s so great about Gretsch is that you can go any way you want: you can do traditional, vintage finishes or you can go crazy with the sparkles and the different colors - it just really works both ways.
"There’s actually two types of sparkle finishes: the traditional drum material - and those are limited in terms of the range of colors we can offer - and then the second kind is sprayed.”
Like many Custom Shops, Gretsch Custom also offers aged finishes. How do vintage Gretsch finishes tend to change over time on the original examples you’ve seen?
“Well, the Gretsch oranges vary a lot and the white finishes always yellow with age. Even some of those old [Silver Jet] 6129s, that sparkle top would yellow over time - but that was just the clear nitro on the top that was ageing.”
What are the most in-demand designs you make, in general terms?
“It’s White Penguins or variations on that, actually - it’s kind of always been that way. Plus Duo Jets to an extent.”
When it comes to pickups and electronics, plenty of variations on the classic Gretsch designs are available at the moment. What do customers tend to ask for on Custom orders?
“Our standard pickup is a TV Jones Classic, but they also came out with those Ray Butts Ful-Fidelity pickups, too, so we’re finding that we’re putting a lot of those on - people are asking for those, plus Power’Trons and Super’Trons, too. But the standard is the TV Jones Classic.
"The pots are 500k pots, and we use the Switchcraft switches. You always have the master volume, then Gretsch added the standby switch back in the early '60s. Some dealers still want a lot of switches and a lot of pickups. Rocky [Schiano], from StreetSounds NYC, he started the three-pickup thing that you might have seen in some of our guitars.
"At one point he said, ‘Can you put a fourth pickup on there?’ but I said, 'Get out of here. Leave me alone [laughs]!'”
Jamie Dickson is Editor-in-Chief of Guitarist magazine, Britain's best-selling and longest-running monthly for guitar players. He started his career at the Daily Telegraph in London, where his first assignment was interviewing blue-eyed soul legend Robert Palmer, going on to become a full-time author on music, writing for benchmark references such as 1001 Albums You Must Hear Before You Die and Dorling Kindersley's How To Play Guitar Step By Step. He joined Guitarist in 2011 and since then it has been his privilege to interview everyone from B.B. King to St. Vincent for Guitarist's readers, while sharing insights into scores of historic guitars, from Rory Gallagher's '61 Strat to the first Martin D-28 ever made.