Everything you need to know about acoustic guitar neck joints – how they work, and why they matter for your tone
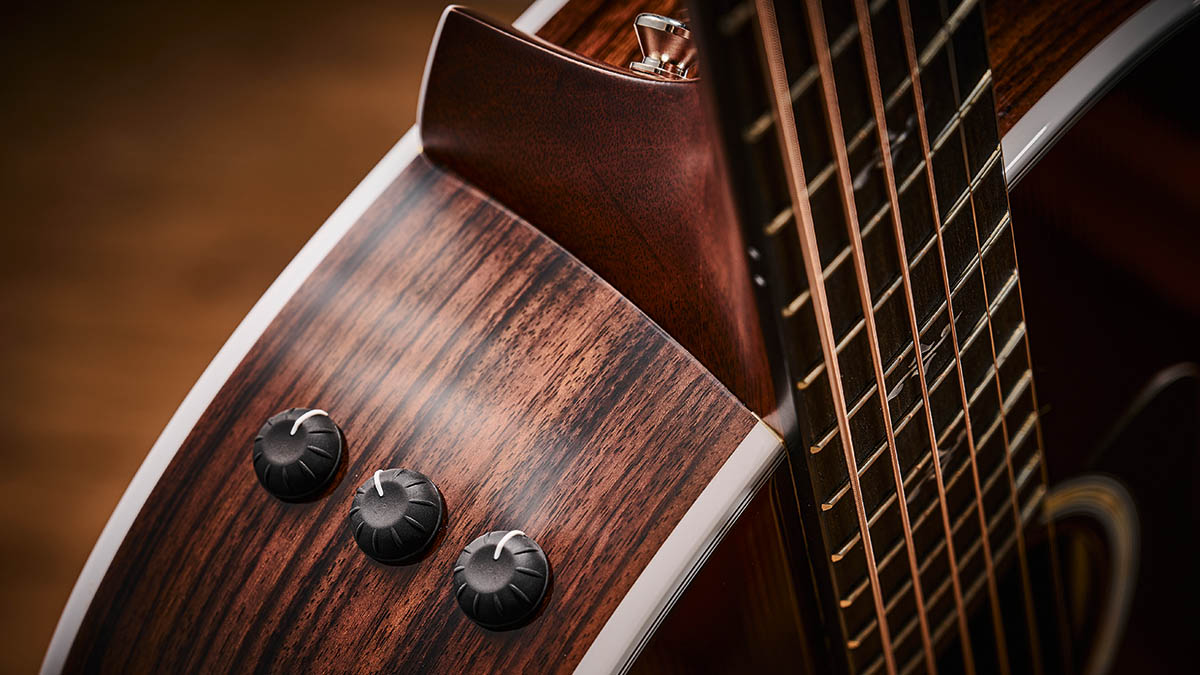
It’s hard to pinpoint the time when the belief that glue is good and bolts are bad took hold. The cynic in me might suggest that it was instigated, or at least propagated, by some traditionally minded guitar manufacturers in response to a Californian company that sent shockwaves through the industry in the early 1950s.
By the 1970s, sustain worshippers were even making the case for dispensing with neck joints altogether and making guitars from continuous lengths of wood. The main beneficiaries of this simplistic thinking were Fender fans, who could pick up vintage examples of their beloved instruments for next to nothing.
Even if you buy into the argument that glued necks offer superior sustain, it’s harder to make the case for superior tone. This is obviously the case with electric guitars, since the pickups and hardware have such a profound impact on the overall sound of the guitar.
But try comparing the unplugged tonal qualities and sustain of a 50s-style lightweight swamp ash Telecaster with a leaden Les Paul Custom from the 1970s, and an unbiased ear might conclude that the former wins on both counts. The question is whether these findings also apply to acoustic guitars.
Dovetailing
For decades the dovetail joint was by far the most common method of uniting bodies and necks. Many of the earliest guitars were made by luthiers with a background in violin, viola and cello building, so dovetail neck joints carried over to guitars – outside Spain, at least. Heritage manufacturers, including Martin, Lowden and Gibson, still use traditional dovetails for high-end vintage-inspired models.
While glued dovetails can remain structurally sound for several decades, almost every acoustic will require a neck reset eventually
The recess in the neck block and the dovetail itself are both angled along their mating surfaces. When the joint is accurately cut and adjusted, pressing the neck into the block actually pulls the heel tightly against the body. Glue is applied to make this firm friction fit permanent when the neck and body are joined.
Dovetail proponents argue the tight physical contact promotes tone transfer between the neck and body, so they both resonate ‘as one’. To facilitate this tone transfer, glues that set crystal hard, such as Titebond Original aliphatic resin and traditional hot hide glue, are also advocated.
All the latest guitar news, interviews, lessons, reviews, deals and more, direct to your inbox!
While glued dovetails can remain structurally sound for several decades, almost every acoustic will require a neck reset eventually. This may be because the glue starts to fail and a gap opens up between the heel and body.
It can also be because string tension has deformed the body and the guitar’s geometry needs correcting. Either way, a neck reset becomes unavoidable when the action becomes excessively high and there’s insufficient saddle height to compensate. Martin always factored this into its builds by finishing necks and bodies separately.
But resetting a glued-in neck is a skilled process that can require finish touch-ups and expense for the owner. Many guitars are sent back to the original manufacturer for neck resets, and some may even be done under warranty. Eventually, guitar builders started considering alternative neck attachment methods that would simplify the reset process and minimise the risk of damaging the finish without any compromise in tone.
Glueless
For many modern acoustic guitar manufacturers, the ideal neck joint would be quick to set and reset, and offer equivalent or even superior sonic qualities to traditional dovetails. And that’s precisely what companies as diverse as Taylor, Bourgeois, Collings, Atkin, Taran and Furch have set out to achieve – albeit in individual ways. And yes, they’re all using bolts to secure glueless joints.
Of all the factors generally considered crucial to bodies and necks resonating ‘as one’, contact area and joint tightness generally top the list. A well-executed dovetail certainly creates a tight bond, but the mating surfaces are actually quite small.
Bolt-on neck attachment means that the builder doesn’t have to rely on the joint itself to achieve the bond. Consequently, the mating surfaces can be larger and torqued metal bolts can exert far more pressure than wedging two pieces of wood together. Some manufacturers, such as Taylor, even attach the fretboard extension using bolts, but others prefer glue.
Our recent visit to the Furch factory provided an introduction to its CNR (Composite Neck Reinforcement) System, a cutting-edge example of modern acoustic guitar construction. It includes a cast ‘L’ shaped aluminium alloy part that’s tightly set into a CNC-routed recess in the heel.
This part is also tapped for bolts. According to Furch’s Martin Kondelčík, “the casting weighs just 66 grams and the thinking was to have the heel as thin as possible for players who use higher positions on the neck to have a greater level of comfort”.
The solidity of the bracket also allows Furch to use a far smaller neck block, which allows the soundboard around that area to resonate more freely. And on the very rare occasion that a Furch needs a neck reset, it takes about 15 minutes.
Joint Efforts
When researching this article, I read several advocates of the traditional dovetail trotting out the “only metal parts that belong on an acoustic guitar are the strings” trope. If that’s the case, then I’d suggest commissioning a steel‑string acoustic built with no truss rod or fretwire, and wooden friction pegs instead of tuners, and see how that works out…
Dovetail proponents argue the tight physical contact promotes tone transfer between the neck and body, so they both resonate ‘as one’
It’s surely implausible that the majority of the world’s finest acoustic guitar manufacturers would knowingly be making inferior-sounding instruments simply to streamline neck resets.
Granted, hand-fitting necks with dovetails and animal-protein glue has a certain romance, and it’s a thing of beauty for anyone building a handful of guitars per month. But CNC-routing equipment and well-crafted bolted joints offer consistent quality and all the other benefits for larger manufacturers who don’t have the luxury of time.
Of all the construction methods separating great-sounding acoustic guitars from ordinary ones, the evidence suggests that having a glued or bolted neck should no longer be considered a deciding factor.
Three innovative acoustic neck joints to audition
Furch Yellow Deluxe GC-CR
Furch’s CNR neck design as found on this GC-CR offers a dual-action truss rod. But it does so by using a lightweight carbon casing that surrounds the truss rod along its entire length.
Furch claims this increases resistance to neck deformations by 90 per cent, and because of the strong rigidity, there’s no need for additional reinforcement, meaning the whole system only adds just under 30 grams – compared with common truss rod systems – to the weight of the guitar.
Martin SC-10E
The Martin SC series makes use of a couple of neck joint features to radically improve upper-fret access. First, there’s an internal block containing a two-way truss rod, but it also includes Martin’s linear dovetail joint.
Externally, the heel is scooped and works in conjunction with the deep cutaway and neck barrel to remove the physical barrier of a traditional heel.
Taylor American Dream AD17E Blacktop
Taylor’s bolt-on neck design not only promises complete vibration transfer (it actually boasts that it’s better than glued necks), but it also allows the neck angle to be set – and reset over time – by someone who knows what they’re doing.
That’s because the glueless design means the neck can easily be removed, and using Taylor’s neck-angle spacers, you can get the best performance from your guitar throughout its life.
Huw started out in recording studios, working as a sound engineer and producer for David Bowie, Primal Scream, Ian Dury, Fad Gadget, My Bloody Valentine, Cardinal Black and many others. His book, Recording Guitar & Bass, was published in 2002 and a freelance career in journalism soon followed. He has written reviews, interviews, workshop and technical articles for Guitarist, Guitar Magazine, Guitar Player, Acoustic Magazine, Guitar Buyer and Music Tech. He has also contributed to several books, including The Tube Amp Book by Aspen Pittman. Huw builds and maintains guitars and amplifiers for clients, and specializes in vintage restoration. He provides consultancy services for equipment manufacturers and can, occasionally, be lured back into the studio.