35 years of Fender Mexico: a timeline
How Fender's Mexican plant went from converted church with a handful of employees to the powerhouse facility behind some of its top-selling instruments
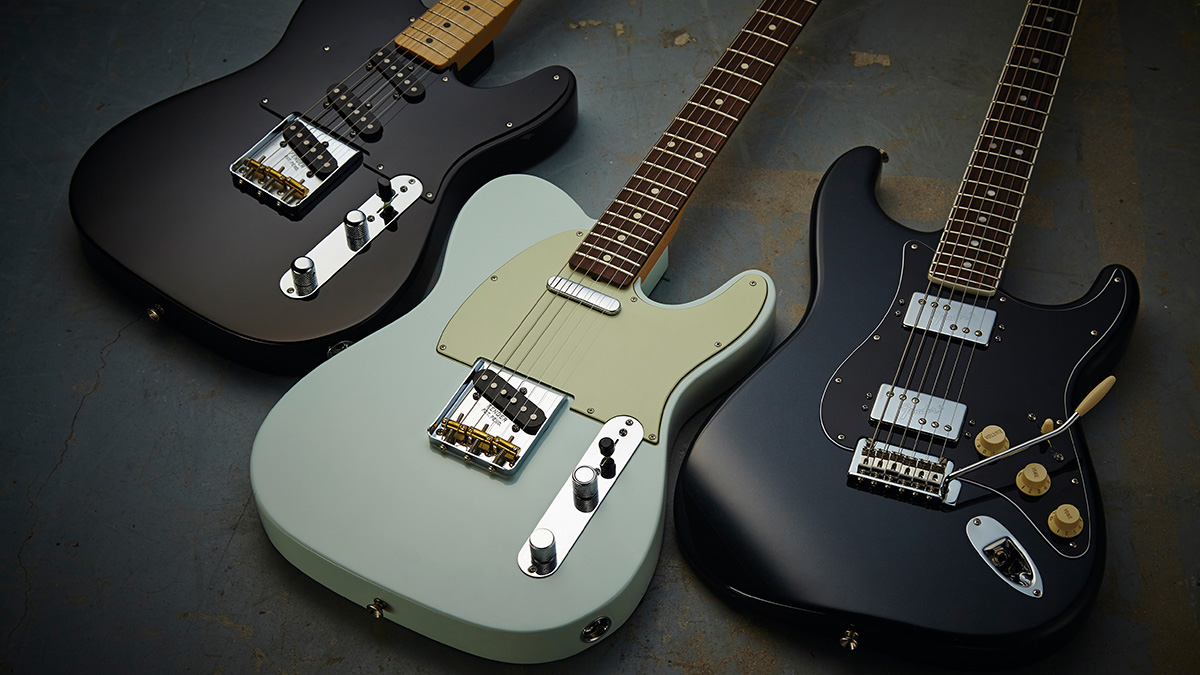
If you are reading this and you play an electric guitar, the chances are you will have at one point played an instrument that was made in Fender’s Mexican factory at Ensenada.
The guitar world as we know it is being shaped by guitars to emerge from Fender Mexico; Ensenada is the production behemoth behind top-selling lines such as the Player, Player Plus, and the retro-inspired Vintera series.
But as this timeline shows, it wasn’t always thus. Located just over the border from the Corona factory in California, the Ensenada facility had humble origins, operating out of a converted church, before the intervention of Fender’s Japanese partner, Fujigen, help realize the potential of Fender Mexico.
Thirty-five years on, it is now at the forefront of Fender’s biggest launches, as the firm diversifies its lineup with the hopes of broadening its customer base.
This is its story.
1987
Fender’s new factory was established in Ensenada, Mexico, just across the California–Mexico border and about a three-hour drive from Fender’s existing Corona factory.
Fender’s previous owner, CBS, had used Mexican firms for packing and making strings, but in 1985, CBS sold Fender to a group led by Fender’s president, Bill Schultz, and various new plans were made.
All the latest guitar news, interviews, lessons, reviews, deals and more, direct to your inbox!
A few years later, a company engineer, Bashar Darcazallie, went to Mexico and set up low-key manufacturing in a converted church in Ensenada. At first, five employees spent their time packing strings. However, as demand for Fender guitars increased during the late ’80s, Fender realized there was scope to make instruments, too, in Mexico.
1989
The Mexico factory moved from its original site at the converted church to the location it still occupies today, on Calle Huerta at the southern edge of Ensenada. Fender began to produce amplifier sub-assemblies at the new site.
1990
Fender had enlisted the help of Fujigen, the firm that made Fender’s guitars in Japan, and the two companies had formed a joint venture, F&F, to develop a guitar manufacturing facility at Ensenada.
Key people were brought in from Fujigen’s plant in Japan to train workers at the new Mexican guitar factory, modeling the processes and layout on the factory back in Matsumoto.
Bill Mendello, who was CEO at Fender in 2011 when we talked, told me about the transition.
“Fujigen brought their machinery with them, plus five or six people,” he said. “We opened up our Mexican operation, and Fujigen trained the people, using their techniques. So the manufacture of guitars in Mexico was more Japanese-like than it was US-like. We had a few people from the USA help them, but for the most part the training, the techniques, the painting – all were Japanese.”
1991
Fender’s first price list to show Mexico-made guitars was dated January 1st 1991. Each instrument on Fender price lists has a unique model code number that, among other things, indicates country of origin, usually in the first three digits, and for Mexico at this period the code was 013 or 014.
The list revealed Mexico’s first Fender guitars: the Standard Stratocaster, Standard Telecaster, Standard Precision Bass, and Standard Jazz Bass, all previously sourced from Japan.
The new Prodigy guitar and bass were officially US-made, but they did receive some attention at the Mexico factory. They had sharp-horned offset bodies and marked the latest attempt by Fender to compete with the popular superstrat-style instruments of the day.
1992
By now, the Mexican factory was assembling around 175 Fender Standard Stratocasters each day alongside various other models. Three years later, it had a daily capacity to produce some 600 instruments in total.
Dan Smith, who headed Fender’s electric guitar team at the time, told me later: “The original plan was for Mexico to make products for export to the USA and other parts of the world, plus a lower-priced line of product for the Japanese market. This was Fujigen’s plan for combating the production being lost by Japan to Korea.”
The F&F joint venture between Fender and Fujigen was a finite affair. “The product Mexico manufactured for the Japanese market didn’t meet the price-points that Fujigen were attempting to hit,” Smith said, “and the quality was not initially good enough for the Japanese market.” Fender bought out Fujigen’s interest and successfully continued alone to develop the Mexico plant.
As we’ll see, in the years that followed, the Mexico factory became an important part of Fender’s manufacturing capability. But some people still don’t realize that it wouldn’t have happened were it not for essential help at its birth from Fender’s Japanese colleagues.
1994
Following a devastating fire in February, the plant was rebuilt, in the process providing twice the space as the destroyed buildings. Later in ’94, the first Mexican models for Fender’s secondary Squier brand appeared, the budget poplar-body Standard Stratocaster, Standard Telecaster, Standard Precision Bass, and Standard Jazz Bass.
Also this year, the first two Mexican-made Fender signature models were produced: the Richie Sambora Standard Stratocaster and the Stu Hamm Urge Bass Standard. Two years later, the James Burton Standard Telecaster became the first Mexican-made signature Tele.
1997
Mexico’s new Deluxe series were versions of regular Fender models, but often with non-standard feature sets. Examples included the Nashville Tele, with its Strat center pickup and five-way switching, and the HSS-loaded Fat Strat, introduced in 1999 with large headstock and S-1 switching.
1998
Retro fever was growing at Fender, and it resulted in a couple of “new” Mexico-made designs that had the vibe, at least, of older instruments. The Toronado was not unlike the recent Squier Jagmaster, boasting a Jaguar–Jazzmaster style body with covered humbuckers and Gibson-like controls.
The Cyclone was a Mustang derivative, adding a bridge humbucker plus single-coil and a Strat-like vibrato.
2001
At the Mexico factory, sub-assembly work for Guild acoustic guitars began. (Fender owned the Guild brand between 1995 and 2014.) Also, production started at Ensenada for the Fender Cyber Twin, a tube/solid-state modeling combo.
2006
Fender had for some time been sending Master Builders from its Custom Shop to the Mexico factory to offer advice and guidance, but this year one of those builders, Chris Fleming, designed a guitar for production at Ensenada.
The result was the Classic Player Baja Telecaster, which added fashionable modern twists to a vintage-flavored core, including its Twisted Tele neck pickup and S-1 switching. The “Baja” name for this model derived from Ensenada’s location in the Mexican state of Baja California.
Other Custom Shop-designed models in Mexico’s Classic Player series included a 50s and 60s Stratocaster.
2007
When Fender came to consider a Joe Strummer Telecaster model, at first the idea was to make a precisely detailed Custom Shop Tribute model. However, the team decided this felt contrary to the spirit of Strummer’s work with The Clash.
The result was a more affordable Mexico-made guitar, significant also for the catalogue name of its ravaged finish, described as “Custom Road Worn.” This was the Mexico plant’s new take on the Custom Shop’s popular “Relic” aged finish.
Fender’s Justin Norvell told me that Joe’s original old Tele was in a battered and rusty state.
“We said to the Mexico factory: Can you make it look like this, but dialed down and more refined?” said Norvell. “They absolutely did that. And a few years later, we came out with our Road Worn series from Mexico.”
It was in 2011 that Fender first offered Ensenada’s Road Worn Strats and Teles. Later, these would be grouped as part of the Classic series, in 2015, and the Vintera series, in 2020.
2012
The first Mexican-made Jackson, the Dinky DK2M, was produced in the factory’s new Specialty Brand area. (Fender acquired the Jackson brand back in 2002.)
2015
Fender launched its first signature guitar for a Latin artist, the Sergio Vallín Artist Series Signature, and the instrument was manufactured at the Ensenada factory. Vallín is the guitarist in the Mexican rock band Maná, and for the body of his signature model he squeezed a little more from an offset Strat shape.
That body featured HSS pickups, stripped-down controls, including a push-pull on the volume for direct-to-humbucker routing, and a five-way rotary selector.
2018
Mexico’s Player series was introduced, replacing the earlier Classic models. In a recent “Best Stratocasters” guide, Guitar World said: “The affordable Player series has fast become one of the most successful lines to ever come out of the Ensenada, Mexico factory.
“These beauties are available with options for HSS or HSH pickup configurations and even locking Floyd Rose tremolos, but it’s the classic Buttercream Strat with the traditional SSS configuration that takes it for us. Screams pure Fender.”
Player Plus versions would be added in 2021, replacing the Deluxe series.
2019
Following Fender’s 2018 US-made Parallel Universe series of mashup models, it was Mexico’s turn to mix and merge with the Alternate Reality series.
Models included the Tenor Tele, a scaled-down four-stringer; the Powercaster, with its aggressive Jazzmaster–Jag vibe; the Meteora, a kind of space-age elongated Jazzmaster; and the Sixty-Six, a Strat derived from two scaled-down Jazz Bass bodies.
Also this year, Fender introduced the Mexico-made Vintera vintage-vibe series that included 50s, 60s, and 70s Telecasters and Stratocasters.
2022
Fender Mexico celebrated its 35th anniversary. The company’s recent introduction of the Acoustasonic Player Telecaster acoustic-electric hybrid is a good example of the steady growth of Ensenada’s role within the Fender operation, with this new model type requiring an entire new factory alongside the existing buildings.
Ed Magee, EVP Operations at Fender, said: “The expansion of the Ensenada factory has been a 26-month long journey, but one that’s been completely necessary to make Acoustasonic technology available to a widespread audience of players around the world.”
Magee then neatly summed up the contribution Mexico makes to Fender today, saying: “We have an incredible depth of engineering, operations, and guitar building experience in Ensenada.” Thirty-five years on, that experience is clearly more important to Fender’s production capabilities than it ever has been.