“I thought to myself, ‘Nobody’s done anything with that for at least 25 years. It looks like a piece of medieval torture instrumentation’”: How G7th revolutionized the guitar capo
The British company has sought to give the humble capo a player-friendly future. As with many great ideas, it evolved from a simple question that designer Nick Campling asked himself while playing an acoustic guitar…
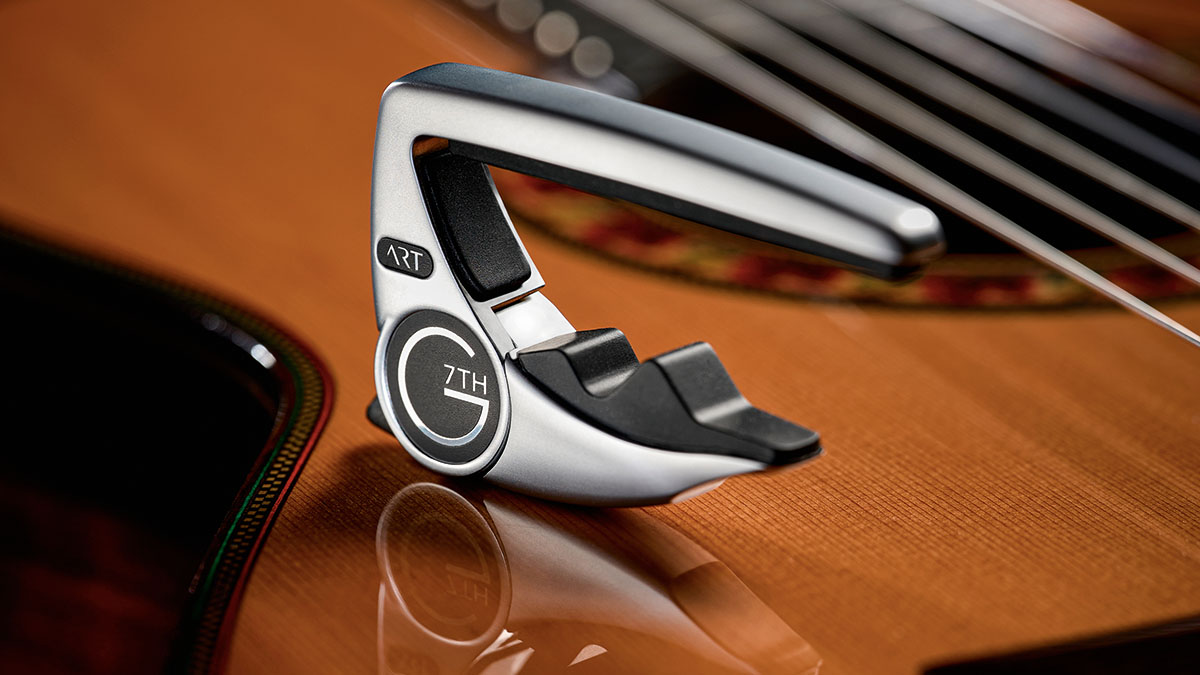
The saying ‘Build a better mousetrap and the world will beat a path to your door’ could easily be applied to G7th capos. Over the years, guitarists have struggled with rudimentary plastic-covered metal bars secured by elastic, or what G7th’s chief designer refers to as items looking like instruments of medieval torture.
The fact is that this was an area of guitar accessorising – and an important one, when you consider how many players rely on them – that had not been re-evaluated for decades.
Since the lightbulb moment that Nick Campling describes below, G7th capos have been sprouting on the guitar fingerboards worldwide, with an impressive roster of players leading the charge.
With a new guitar capo just released that will welcome seven- and eight-string players into the fold, we thought it was high time to tell the company’s story from its outset.
What were the origins of G7th’s journey?
“I had my own design consultancy called 42 Technology near Cambridge in St Ives. And one day, being the bright light I am, I figured out that most of my customers were probably wealthier than I was and perhaps it would be a good idea to develop a product and take it all the way through to market. Nothing happened. Because until you decide exactly what you’re going to do, nothing ever does.
“One day I was playing my guitar, I looked towards my left hand where there was a capo from a well-known make and I thought to myself, ‘Nobody’s done anything with that for at least 25 years. It looks like a piece of medieval torture instrumentation… Let’s do that as an exercise; at least that will get things rolling.’ If I’d been even cleverer, I would have picked on some consumer product that everybody wants, not just guitar players, but never mind!
All the latest guitar news, interviews, lessons, reviews, deals and more, direct to your inbox!
“So we wrote a proper design spec, which included things about aesthetics, weight, ease of use and the sorts of things that you put into a design spec if you’re going to do a professional job.
“I put some of the guys onto it – when we hadn’t got other things to do, because we still had to earn money – so the process took quite a while because we actually hit the market towards the end of 2004 and we formed the company, having already done a bit of work, in 2000. The problem being, as always, there was the day job to cope with, dealing with clients who wanted their projects and wanted them now.”
What were the key elements of the capo you had on your fretboard that day that you thought were ripe for improving?
“Well, a lot of it was about the appearance of it. Because up to that point, they really weren’t consumer products. I can tell you a story that’ll help illustrate that point. Once we had a prototype, I went to a meeting that was a DTI [Department of Trade and Industry] thing.
“We were sitting around a table with maybe 10 people and we were discussing export and the capo ended up on the table being passed around. A lady came in late and sat next to me. She didn’t know anything about what this thing was and it got passed to her and she sat there and she just handled it. About a minute later, she said, ‘This is really nice. What is it?’ That illustrates a really good industrial design.
“I felt that although the particular capo that I had on my fretboard that day was adjustable – so you have control over the pressure – you still had to adjust it each time if you moved it up and down the neck or from guitar to guitar. There was another famous make that had spring action where you had no control over the pressure. Right? What I wanted was to be able to just whack it on, squeeze, done. That was the thinking.”
What would you say was the keystone in your new capo design?
“We came up with a number of mechanical ways of doing a capo that you could just squeeze and would close up and would retain the tension. And the winner was wrapped up in clutch design, which is still in there today.
“It started with the Performance capo; we’ve got a range of them now, but it started with the Performance. At that point in time, I was still working at 42 Technology and so I cast around to find someone who could actually run the thing and sell capos while I carried on with the day job.
A little bit of backlash didn’t matter too much in paper-handling, but it matters a lot if it meant your strings started buzzing. That was the technical problem we had to solve
“Noel Sheehan was in Leicester, running his music store, and I got to know him a bit and he looked at the various prototypes and started off by saying, ‘No, bugger off, Nick. Come back when you’ve got something that works.’ Eventually, we got to something that worked and Noel took it on. I carried on with the technical stuff, so I was overseeing the manufacturing and stuff, which was at that point going on in the Netherlands, and Noel did the commercial stuff from the store in Leicester.
“Then what happened was that in my job at 42 Technology as managing director, I realised that actually I wasn’t having a great deal of fun. I was spending all my time doing sales, and I’m a designer; I like designing things.
“But once you’ve got a machine like a design consultancy, where you’ve got people with PhDs and other guys who are much cleverer than me, you have to keep them working, otherwise the money runs out very, very quickly. And I didn’t enjoy that so much. By that time I’d got other members of the management team onboard and I was basically able to step out and get involved full-time with G7th, which was much more fun.”
Can you go into a little bit of detail about the clutch system at the heart of the Performance capo?
“It’s called a wrap spring clutch. It’s used in a lot of paper-handling type applications: photocopiers and stuff where you’re moving paper around and you’ve got to stop and start things quickly.
“It almost looks like it ought to be a ratchet, but it isn’t. So it’s got a spring wrapped around two hubs and when you turn one of the hubs in one direction, you’re unwinding the spring so it moves.
“Go back the other way and you’re trying to wind the spring up. The big challenge was to remove backlash from that system. You know, a little bit of backlash didn’t matter too much in paper-handling, but it matters a lot if it meant your strings started buzzing. That was the technical problem we had to solve.”
How did you choose the material you were going to use for the capos?
“I mean, obviously, die-casting is a good way to get the shape that you want. It’s fast and it’s relatively inexpensive. We could, in theory, have gone for aluminium, but I wanted some quite diverse and quite thin sections, and zinc flows more easily than aluminium. In the early days, one or two people said, ‘Boy, it’s a bit heavy…’ But it doesn’t weigh that much more than its competitors and I think people like it.
“So aluminium might have been a bit lighter, but zinc gave us the ability to make the shapes. And also, because zinc flows more easily, tooling lasts a bit longer, too.”
Aluminium might have been a bit lighter, but zinc gave us the ability to make the shapes. And also, because zinc flows more easily, tooling lasts a bit longer, too
You mentioned that keeping the pressure on the strings constant was another factor in the design.
“Well, that’s what I mean by backlash. If you close it down, you don’t want it to open up again. So it has to grip straight away and the solution to that is fairly technical. And I’m not going to tell you how we did it! [Laughs] It really just has to close and the clutch has to grip immediately.
“As for the pad that holds the strings down, we started with a TPE: that’s a thermoplastic elastomer and that was fine, it was very good. Later on, we moved production to China for cost reasons and they couldn’t get the particular TPE that we needed. So we moved to silicon rubber. The snag with that is it’s harder to glue, but it is completely inert.”
The original Performance capo has gone through various iterations and upgrades over the years. What sort of changes have you made to the original design?
“Well, that’s part of the problem of being a designer – you kind of never finish! There had been people saying, ‘It’s a bit wide…’ and I looked at the way we made it and felt I could make the clutch a bit smaller. So that became the Performance 2.
“And then the Performance 3 mostly came about because we came up with the Adaptive Radius Technology, or rather a string pad that would adapt to the radius over your fingerboard.
“That’s a bit of an interesting story in itself because, in practice, I installed that into the Heritage [capo] to start with. And the Heritage came out with a system that used a wax capsule behind the rubber. So it was kind of hydraulic. And we even launched it at NAMM.”
“Then we got a notification from a patent agent somewhere saying, ‘Excuse me, you can’t do that…’ And it was in a very obscure patent, but it described exactly what we were doing. So my patent agent phoned me up and said, ‘I don’t know if this is important, but I think you should see this.’ It was important and I went into panic mode, as you can imagine, because we’d sold some.
“What happened was typical of how the mind goes into overdrive when necessary. The information came through on a Thursday and by the following Tuesday, we had a new patent application.
“Because, over the weekend, my brain churned away and at some random time, in the middle of the night probably, I suddenly realised that I could do it mechanically and do away with the capsule and have a system of little cams, which is what we have now and what our patent describes. It was a tricky moment, but it went into the Heritage first and then into the Performance 2.”
The G7th range has now expanded significantly to cover practically all bases with capos for just about every type of guitar – and beyond.
“Yes. The range now includes the Nashville Capo, which is a spring capo because some people will prefer the way that works and they’re prepared to cope with the fact that you’ve not got control over the tension. It’s still a great capo and a lot of people love it and we’re happy enough with that. And we’ve got classical, six-string and ukulele versions of that.
The range now includes the Nashville Capo, which is a spring capo because some people will prefer the way that works and they’re prepared to cope with the fact that you’ve not got control over the tension
“Then there’s a Newport capo, which we use as our ‘this-will-cope-with-anything’ capo. There are all sorts of versions of that: there’s a six-string version, partial capos, a banjo capo. And there’s the 12-string capo, which is the one that we installed our compensated string pad into, which has basically got teeth so all the strings get the same pressure.
“Because of the tooth, the smaller string and the bigger string of the pair are pushed down the same amount because they both start the same sort of distance from the fret. What tends to happen on a 12-string is if you just whack the capo on it, the bass strings get well squeezed and pulled sharp before the treble strings are fretted. So that’s the Newport.
“And then the Heritage is the one that’s a yoke capo and we’ve got a few versions of that. We’ve got a six-string – both standard width and a slightly wider one – and we do a 12-string version of that as well.”
And there’s a new variation of the Performance that has just been released.
“Yeah, the latest has literally just been launched and so I’d like to make a fuss about this one. It’s the Performance capo for a wider neck. So classical guitars, seven-string guitars, eight-string guitars…
“It was launched at Mannheim [Guitar Summit] in September this year. Basically, it’s just a wider capo, it’s got a little bit more length on the top bar, so it makes the Performance capo available to a wider group of players. There’s nothing more brewing at this particular minute. I’m constantly churning, but I feel we’ve got a very good range.”
- For more info, head to G7th.com.
With over 30 years’ experience writing for guitar magazines, including at one time occupying the role of editor for Guitarist and Guitar Techniques, David is also the best-selling author of a number of guitar books for Sanctuary Publishing, Music Sales, Mel Bay and Hal Leonard. As a player he has performed with blues sax legend Dick Heckstall-Smith, played rock ’n’ roll in Marty Wilde’s band, duetted with Martin Taylor and taken part in charity gigs backing Gary Moore, Bernie Marsden and Robbie McIntosh, among others. An avid composer of acoustic guitar instrumentals, he has released two acclaimed albums, Nocturnal and Arboretum.